Defective products are a nightmare for any customer. Such products not only disappoint the customers but also put their lives at risk. At TC_ELLIS, we have always taken the quality of our products very seriously. However, there are sometimes rare incidents when products make it through quality checks without us being aware of the defects.
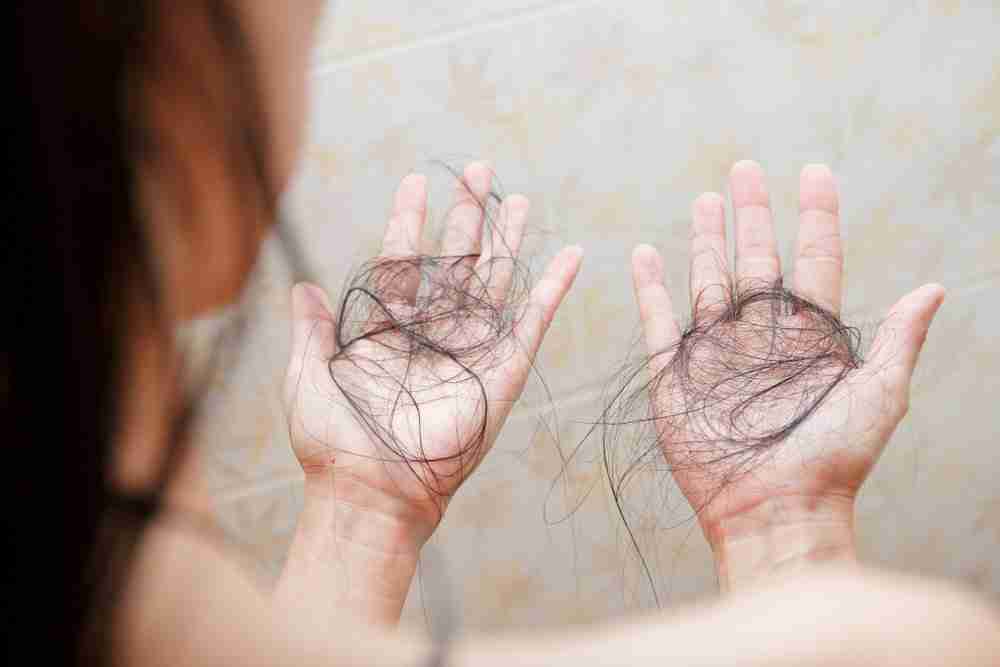
As a responsible company, we take full accountability for such incidents and do everything possible to rectify the problem. If you have received a defective product from us, we sincerely apologize for the inconvenience caused. We want to assure you that we are committed to resolving the issue and ensuring that the product meets the highest quality standards.
In this blog post, we will discuss the steps we take to prevent defective products and what we do when we identify one.
Our commitment to quality
At TC_ELLIS, we understand that quality is of utmost importance to our customers. Therefore, we have implemented stringent quality control measures at every stage of our manufacturing process. From the selection of raw materials to the final product inspection, we leave no stone unturned to ensure that our products meet the highest quality standards.
Preventing Defective Products
Despite our best efforts, there are occasions when a product may make it through the manufacturing process with a defect. We recognize that such incidents not only affect our customers but also damage our reputation. Therefore, we have taken several measures to prevent defective products from reaching our customers.
1. Raw Material Selection - We pay particular attention to the selection of raw materials. We only choose suppliers that meet our stringent quality standards for raw materials.
2. Quality Control Inspections - Our products go through several quality control inspections before they leave our manufacturing plant. We have a team of highly skilled inspectors who conduct thorough checks on each product to ensure that it meets our quality standards.
3. Product Testing - We have fully equipped laboratories where we conduct tests on our products to ensure that they meet regulatory requirements and our quality standards.
4. Employee Training - We constantly train and educate our employees on quality control measures to ensure that they are well-equipped to identify and prevent defective products.
Responding to Defective Products
If we identify a product defect or if a customer reports a defective product, we take prompt action to rectify the issue. Our response to a defective product typically involves the following steps:
1. Investigation - We investigate the problem to determine the root cause of the defect. We take into account any customer feedback or observations to ensure that we identify the problem correctly.
2. Correction - Once we have identified the problem, we take appropriate measures to correct it. This could involve re-manufacturing the product, replacing the defective part, or issuing refunds or product recalls.
3. Prevention - We take steps to prevent similar incidents in the future. This could include re-designing the product, altering our manufacturing process, or re-training our employees.
Conclusion
At TC_ELLIS, we take the quality of our products very seriously. We understand that our customers rely on us to provide them with products that are safe, reliable, and of the highest quality. Therefore, we have implemented several measures to prevent defective products from reaching our customers. If you have received a defective product from us, rest assured that we are committed to solving the problem and ensuring that you are completely satisfied with our response.
Keywords: Defective Product, TC_ELLIS, Quality Control, Manufacturing Process, Raw Materials.